The Buzz on Alcast Company
The Buzz on Alcast Company
Blog Article
Fascination About Alcast Company
Table of ContentsThe 10-Minute Rule for Alcast CompanySome Of Alcast CompanyThe Best Strategy To Use For Alcast CompanyHow Alcast Company can Save You Time, Stress, and Money.The 30-Second Trick For Alcast CompanyThe smart Trick of Alcast Company That Nobody is Talking About
The refined difference hinges on the chemical material. Chemical Contrast of Cast Light weight aluminum Alloys Silicon promotes castability by decreasing the alloy's melting temperature and enhancing fluidness throughout spreading. It plays a vital function in permitting elaborate molds to be filled up precisely. Additionally, silicon contributes to the alloy's toughness and wear resistance, making it valuable in applications where sturdiness is important, such as automotive components and engine parts.It additionally enhances the machinability of the alloy, making it simpler to refine into finished products. In this means, iron contributes to the general workability of light weight aluminum alloys.
Manganese contributes to the strength of aluminum alloys and improves workability. Magnesium is a lightweight element that gives stamina and effect resistance to aluminum alloys.
The Ultimate Guide To Alcast Company
Zinc boosts the castability of aluminum alloys and assists manage the solidification procedure during spreading. It improves the alloy's stamina and firmness.
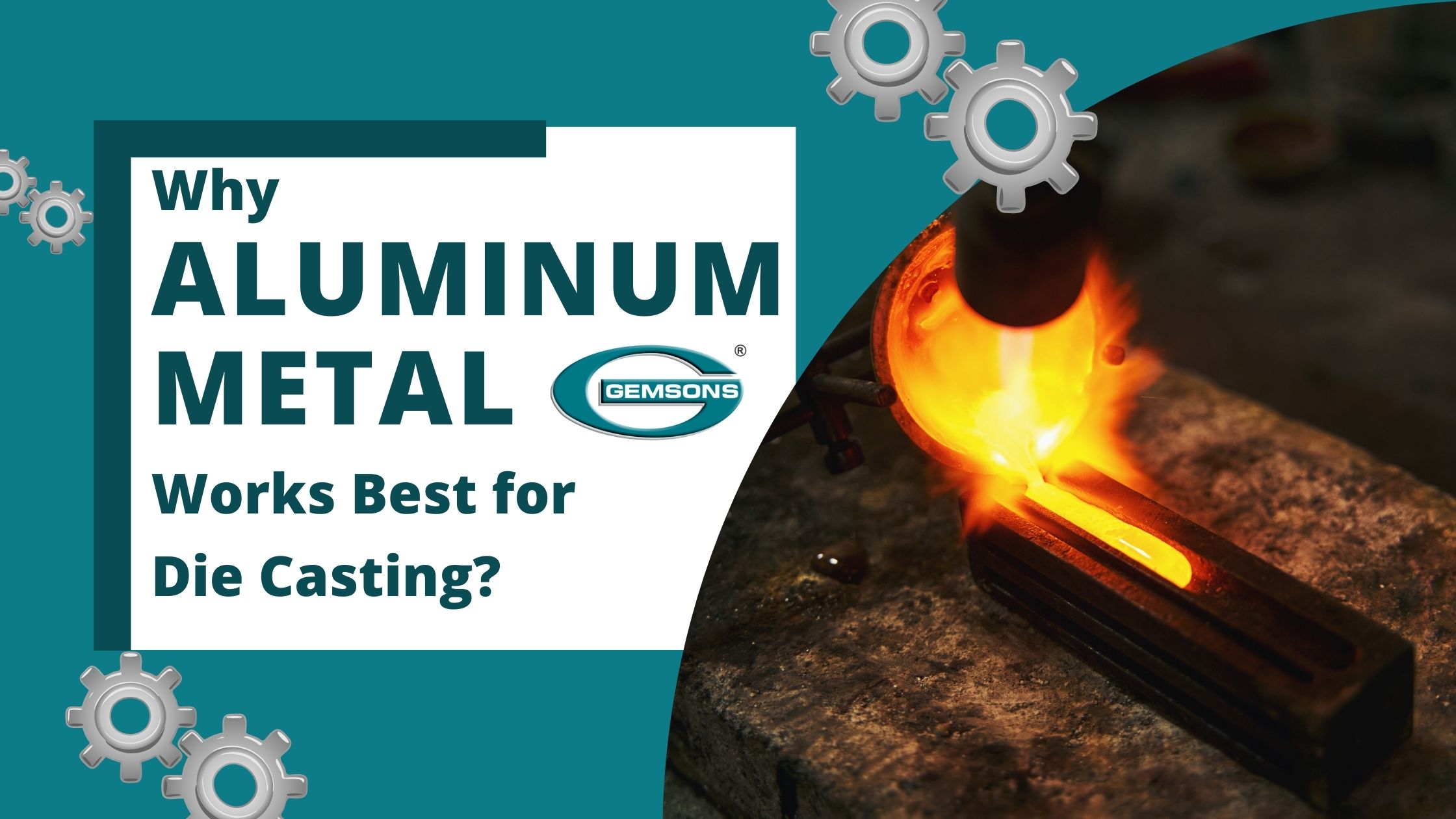
The main thermal conductivity, tensile toughness, yield toughness, and prolongation vary. Select ideal resources according to the performance of the target product produced. Amongst the above alloys, A356 has the highest possible thermal conductivity, and A380 and ADC12 have the most affordable. The tensile restriction is the contrary. A360 has the very best yield stamina and the highest prolongation rate.
Rumored Buzz on Alcast Company

In accuracy casting, 6063 is appropriate for applications where intricate geometries and premium surface area finishes are critical. Instances include telecommunication enclosures, where the alloy's superior formability enables streamlined and visually pleasing styles while keeping architectural stability. Likewise, in the Lighting Solutions market, precision-cast 6063 parts produce stylish and effective lighting fixtures that require detailed shapes and good thermal efficiency.
The A360 displays premium elongation, making it perfect for complicated and thin-walled components. In accuracy casting applications, A360 is appropriate for industries such as Customer Electronic Devices, Telecommunication, and Power Tools.
Our Alcast Company PDFs
Its special homes make A360 a valuable option for accuracy spreading in these industries, enhancing item toughness and high quality. Foundry. Aluminum alloy 380, or A380, is an extensively used spreading alloy with numerous unique qualities.
In precision casting, aluminum 413 shines in the Customer Electronic Devices and Power Equipment sectors. This alloy's exceptional deterioration resistance makes it an excellent option for outside applications, ensuring long-lasting, durable products in the discussed sectors.
The smart Trick of Alcast Company That Nobody is Talking About
As soon as you have determined that the aluminum die casting procedure is appropriate for your project, a crucial following step is making a decision on one of the most proper alloy. The light weight aluminum alloy you choose will significantly influence both the spreading procedure and the homes of the end product. As a result of this, you have to make your decision meticulously and take an enlightened technique.
Figuring out the most ideal light weight aluminum alloy for your application will imply considering a large selection of characteristics. These relative alloy attributes comply with the North American Pass Away Casting Association's guidelines, and we've divided them into 2 classifications. The first classification addresses alloy attributes that affect the manufacturing process. The second covers characteristics influencing the original site properties of the end product.
3 Simple Techniques For Alcast Company
The alloy you choose for die spreading directly influences several aspects of the casting process, like how simple the alloy is to work with and if it is vulnerable to casting defects. Warm breaking, also called solidification splitting, is a regular die casting defect for aluminum alloys that can result in internal or surface-level tears or fractures.
Particular light weight aluminum alloys are much more prone to warm splitting than others, and your choice should consider this. An additional common defect discovered in the die spreading of aluminum is pass away soldering, which is when the actors stays with the die walls and makes ejection hard. It can damage both the actors and the die, so you must seek alloys with high anti-soldering residential properties.
Deterioration resistance, which is already a significant attribute of aluminum, can differ considerably from alloy to alloy and is an important particular to take into consideration depending upon the environmental problems your item will be revealed to (Aluminum Castings). Wear resistance is another residential or commercial property typically looked for in aluminum products and can differentiate some alloys
Report this page